The pharmaceutical industry currently faces a major challenge in taking full advantage of the opportunities presented in large emerging markets. Now, more than ever, pharmaceutical companies need to introduce lean manufacturing techniques that will enhance profitability. As one of the world's leading industrial automation suppliers, Yokogawa is committed to delivering the best possible solutions for your best manufacturing practices.
Details
What is Pharma 4.0?
Pharma 4.0 is a roadmap developed by ISPE for the pharmaceutical industry to introduce "Industry 4.0" (also called Smart Factory).
In Industry 4.0, continuous development is aimed at improving quality and productivity, reducing costs and ensuring supply stability throughout the entire product life cycle. This is primarily accomplished by reformation of business processes through IT innovation and digitalization.
Furthermore, Pharma 4.0 needs to meet not just business performance aims and objectives, but also obligations arising from governmental regulations specific to the pharmaceutical industry.
In other words, Pharma 4.0 can be viewed as leveraging IT capabilities throughout the entire product life cycle to build quality control processes founded on ICH-Q10 Pharmaceutical Quality System (PQS) guidelines.
To realize Pharma 4.0, it is essential to have IT implementation skills for digitalization and a clear vision that incorporates a detailed understanding of pharmaceutical regulations including PQS.
Why is Pharma 4.0 still required?
However, the pharmaceutical industry is caught between the increasing cost of compliance to ensure quality and the need to generate profits.
To move beyond this hurdle, Pharma 4.0 implementation can be of great benefit.
Effective, efficient, and continuous quality improvement efforts based on scientific evidence are necessary (i.e.,POS) throughout the pharmaceutical life cycle and according to that defined in the ICH-Q12 Product Life Cycle Management (PLCM) guidelines.
As a consequence, the compliance cost for quality assurance continues to increase in the pharmaceutical industry.
And in parallel, the industry climate of worsening returns in drug discovery has forced an increased need to extract productivity gains that often include the drug manufacturing process.
To address this idea, the pharmaceutical manufacturing industry has chosen to intensify industrial automation (i.e. Pharma 4.0) and drive business reform through digitalization and in full compliance with pharmaceutical regulatory standards.
Yokogawa's business vision in the pharmaceutical business
Continuously since the 1980s and based on a strategic focus of measurement, imaging, analysis, diagnosis and integration; Yokogawa has offered manufacturing control systems and numerous instruments that support pharmaceutical production processes for active pharmaceutical ingredients (API), drug formulations, and biotechnology applications,
Since 1990s, we have been working on [Industrial Automation] of production in order to realize safe and efficient production by linking the vast amount of information obtained from equipment scattered in the factories and providing various solutions of production management for the utilization.
Beginning around the same time, Yokogawa began also providing live cell imaging solutions that used novel confocal microscope technology to the field of drug discovery and cutting-edge medical research.
By integrating and deepening our core technologies and experience, Yokogawa is developing safer and more efficient autonomous production systems that meet the needs of the pharmaceutical industry, allowing professionals more opportunity to apply uniquely human capabilities such as creativity and innovation to the work-place.
Autonomous production systems will also reduce the reliance on human judgement for decisions regarding pharmaceutical manufacturing, quality testing, documentation and release, thus providing greater consistency and time for staff to focus on higher-level productivity efforts.
We have defined this industry "world-view" as Bio Industrial Autonomy (BIA) and made its realization a mission of the Yokogawa pharmaceutical business organization.
Thus, we will contribute to Pharma 4.0 through the implementation of BIA.
For more information about BIA, click here.
Effects of Pharma 4.0 Implementations
An advanced network that connects information obtained from research, development, and manufacturing will provide a variety of positive effects by enabling complementary utilization of information from each department.
As an example, the concepts of Quality-by-Design (QbD) and Continuous Production can be enabled for new drug development and manufacturing processes. These can have the following effects:
- An early identification of Critical Process Parameters (CPP) and Design Space (DS) through data analysis.
- Monitoring of Critical Quality Attributes (CQA) by using Process Analytical Technologies (PAT) such as soft sensors.
- Promotion of Real-Time Release Testing (RTRT) of intermediates or finished products by Critical Quality Monitoring.
- An enhanced understanding of product characteristics and manufacturing processes based on accumulated data.
- Rapid response time to abnormalities and deviations based on data-driven risk assessment by improving accessibility to data
- Continued process improvement through feedback and reduction of time and costs involved in developing new drugs and manufacturing processes.
This communication network and cycle enhances competitiveness and fosters continued business growth.
Yokogawa's total solutions to realize Pharma 4.0
Please refer to the following product groups that provide solutions to pharma customer problems and can help you with your goal attainment.
Yokogawa Solution List |
|
---|---|
【Production scheduling】 | FLEXSCHE |
【Production, sales and cost management】 | mcframe |
【Quality management】 | OpreX Laboratory Information Management System |
【Environmental monitoring】 | OpreX Environmental Monitoring System |
【Equipment maintenance and management】 | eServ |
【Process database】 | PI System |
Exaquantum | |
【Procedural automation】 | Exapilot |
【Production process monitoring and control】 | Collaborative Information Server (CI Server) |
CENTUM VP | |
Field Instruments | |
【After-sales service business support】 | ServAir |
Environmental Monitoring Compliant with Pharmaceutical Regulations
OpreX Environmental Monitoring System collects, measures, and stores data such as temperature and humidity as well as other management data to monitor the environment in pharmaceutical manufacturing area, quality control area, and storage area.
Major features
Data Integrity
- Meets ALCOA+ requirements
Data Collection and Long-term Storage
- Long-term storage of collected data in recorders that are FDA 21 CFR Part 11 compliant
Real-Time Data Monitoring
- Monitor measured data and alarms using the monitoring software
Centralized Management for Login User
Centralized management of user names and passwords using servers on the network is possible through active directory.
- Centralized management of user name/password in data server and recorders
- User login access control
Packages
Data Management Package
Centralized management of the recorded data file
Access Control
Users are assigned to groups and are given access privileges based on the group they belong to.
Only authorized users can login to the system and search and browse through data.
Audit Trails
All file operations by authorized users are recorded in an audit trail file.
- File operations (archive, delete)
- Backup and restore
Configuration Tool
Adminstrator configures the Data Management Package using this tool.
- Register new recorders
- Register new users
- License management
GA10 Real-time Monitoring Software
Monitor measured data in real time
- Measured value display (trend display / digital display)
- Alarm notification on the screen
- Monitor data for each measurement group
Universal Viewer
Dedicated viewer software for browsing recorded data
- Display recorded data
- Supports latest OS and offers best viewing quality
- Supports 7 languages
Paperless Recorder
SMARTDAC+ Series
Measure and record a variety of data
- Add I/O modules as needed
- Wide variety of powerful display functions
- A full range of network functions
Advanced Security Function
Electronic recording of data is compliant with pharmaceutical regulations
- Logical security
- Audit trail function
- Secure data storage in binary format (fraud proof)
- Dedicated viewer software
Customer Challenge
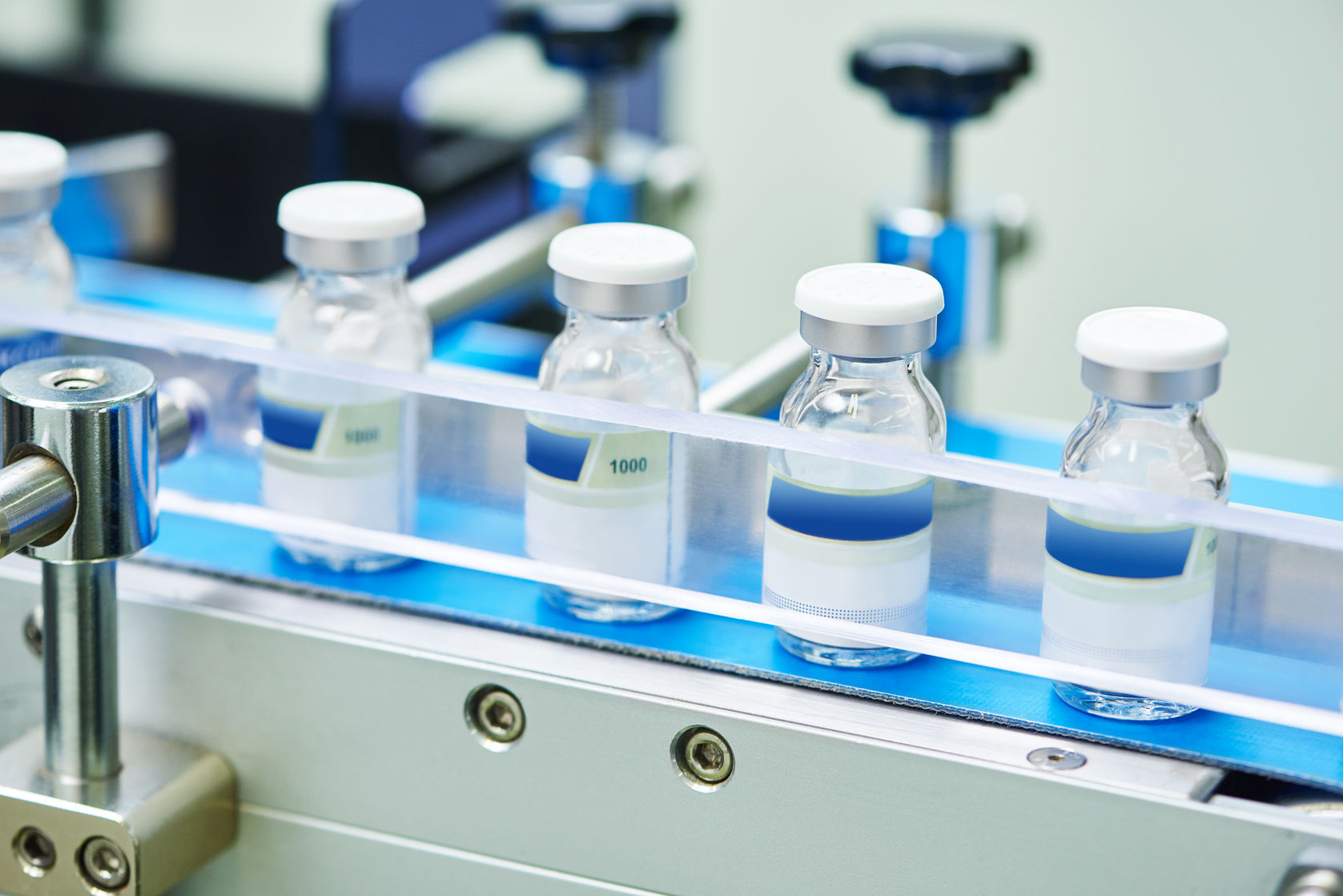
Keeping up with a changing marketplace
Pharmaceutical manufacturers are under pressure to keep up with changes such as the shift to low-cost drugs in emerging markets and the demand for drugs that effectively satisfy unmet medical needs. To operate at a profit, manufacturers are looking for ways to improve efficiency and increase productivity. Lean manufacturing is the key.
Our Solutions
Yokogawa's Leading-Edge Automation Solutions
Our solutions enable plantwide integration and lifecycle optimization at pharmaceutical plants. Here are some pharmaceutical applications for which Yokogawa provides comprehensive automation solutions and has a global network of experts at your service.
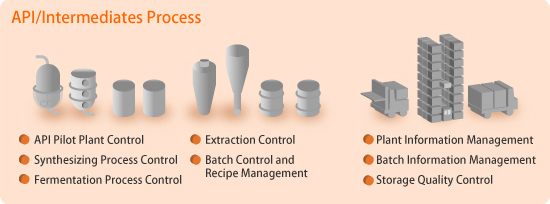
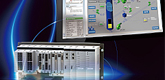
Production Management and Batch Control for Multipurpose Plants
The production of active pharmaceutical ingredients (API) involves batch processes, some of which produce multiple products for a variety of purposes. This necessitates the use of a comprehensive batch control system. The CENTUM VP integrated production control system supplies batch functions based on the ISA-88 batch process control standard and complies with the FDA's 21 CFR Part 11 requirements.
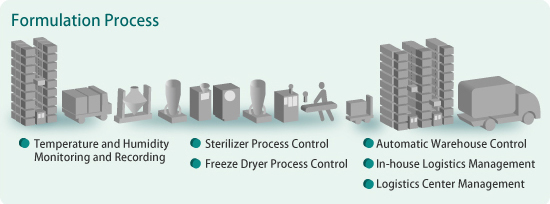

Paperless operations based on 21 CFR Part 11 are becoming more common in the pharmaceutical industry.
The SMARTDAC+® GX/GP Series Paperless Recorders support electronic recording functions that meet the requirements of Part 11. Electronic signatures can be added to the stored data. Yokogawa can offer complete installations with all essential validation documents.
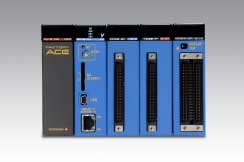
Stable control for product quality assurance
The sterilization and freeze drying processes require high resolution and accurate temperature control in order to assure product quality. The FA-M3V IT machine controller is a high-performance programmable logic controller (PLC) that combines very high processing speeds with stable control features.
Customer Challenge
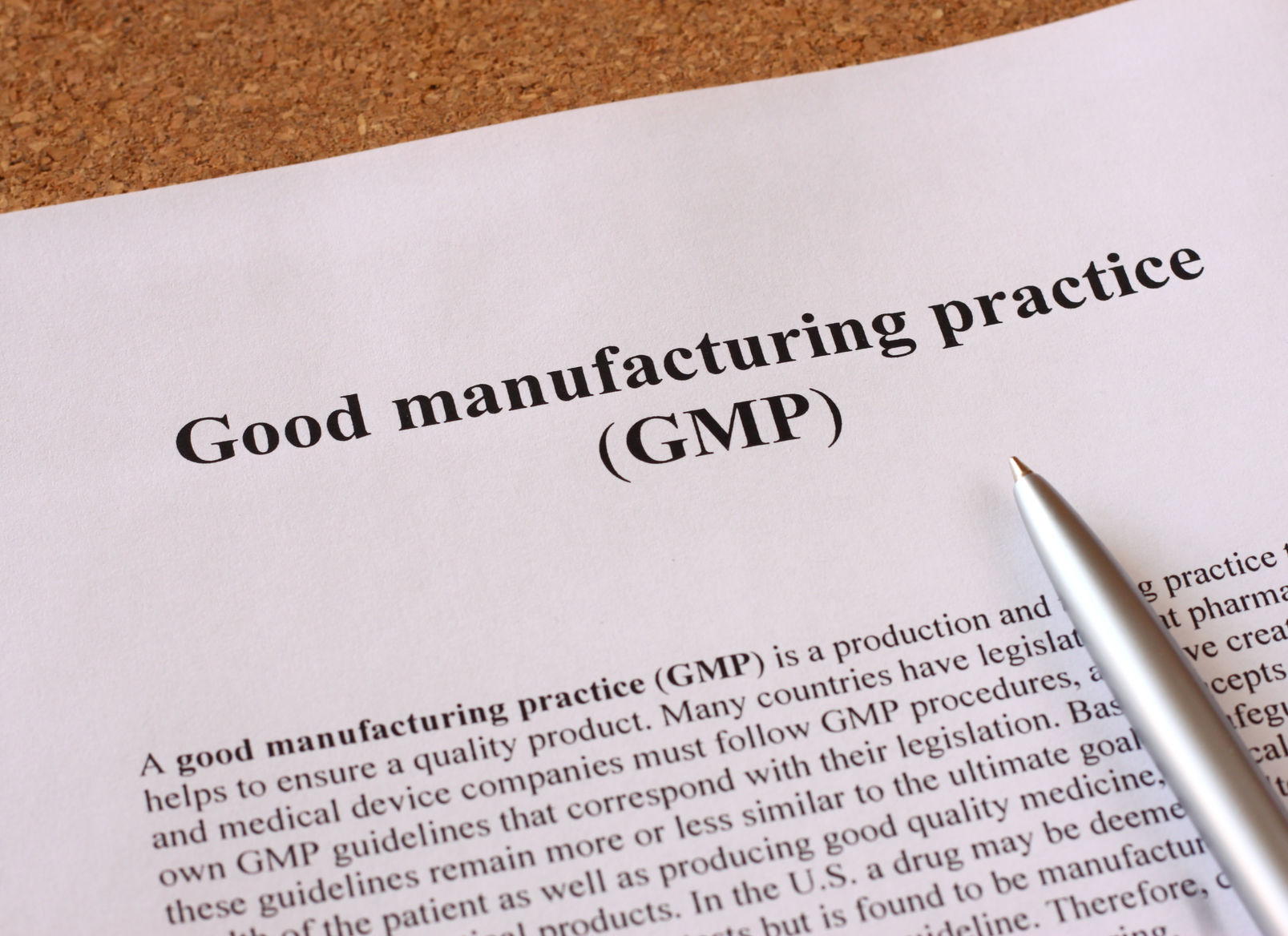
Compliance with globalized regulations and guidelines
Pharmaceutical companies operate in a global marketplace and the industry is encouraged to comply with international initiatives such as the PIC/S GMP Guide and the ICH Guidelines. GMP facilities need to follow established best practices and automated production equipment and computer systems are expected to adopt current computerized system validation (CSV) practices such as GAMP.
Our Solutions
Assuring the Production of Quality Pharmaceutical Products
Over the years, Yokogawa has successfully realized numerous projects in compliance with Good Automated Manufacturing Practice (GAMP). Under a project validation plan (PVP) that follows the V model described in the GAMP guide, experienced Yokogawa engineers deliver outcomes for the functional specification, design specification, implementation, factory testing, and site acceptance testing phases. The verification and test results, including the installation and operational qualifications (IQ /OQ), serve as objective indicators for determining if project requirements have been met.
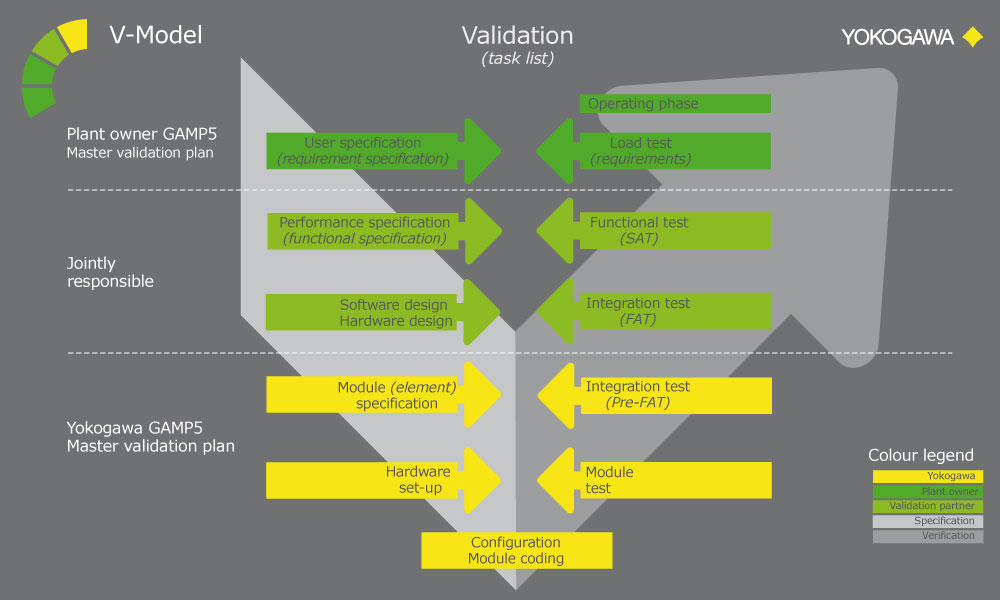
Customer Challenge
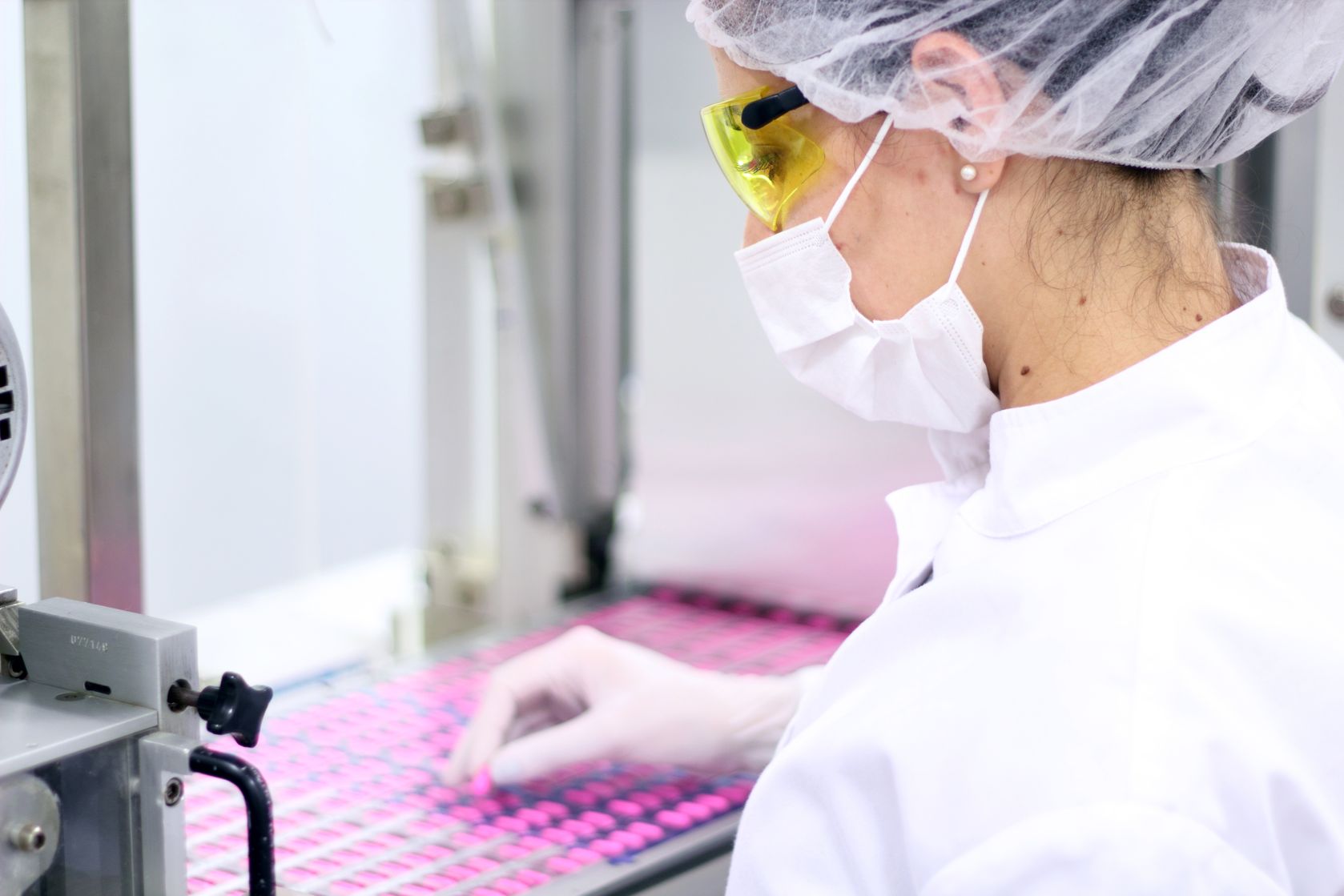
Need for a more rigorous approach to ensure product quality
With pharmaceuticals, a rigorous scientific approach is needed to ensure product quality. The ICH quality guidelines call for a quality-by-design (QbD) approach in pharmaceutical development and manufacturing. Manufacturing facilities face the challenge of implementing innovative technologies such as process analytical technology (PAT) and are expected to introduce real-time release (RTR) testing.
Our Solutions
Yokogawa PAT Solution to Real-Time Release Testing (RTRT)
Yokogawa's approach to the development of process analytical technology (PAT) solutions relies on real-time monitoring of critical quality attributes (CQA) to achieve lean manufacturing. Online quality attributes can be directly monitored by means of near infrared (NIR) analysis. Another approach is the use of process modeling technology to monitor process health.
Resources
- Highlyadvanced biopharmaceutical plant uses CENTUM, VP Batch, Exaquantum and PRM.
- Total system integration for large-scale biotech production facility.
- Yokogawa provides CENTUM VP with Batch Recipe Management Package for new fine chemical plant.
- Yokogawa's CENTUM VP complies with the requirement of Good Automation Manufacturing Practices(GAMP).
Senju Pharmaceutical selected Yokogawa's Oprex EMS to ensure manufacturing quality.
EMS helps improve operational efficiency while complying with GMP and other guidelines.
- Uninterrupted Medical Oxygen Production with FAST/TOOLS Monitoring.
- Audits are performed periodically, requiring traceability and the keeping of historical records for all batch production activities.
- RotaMASS was chosen to work with weight measurements and/or differential pressure transmitters for extremely accurate measurements.
- The customer recognized the product's advantages: reliability, accuracy, guaranteed draining system, easily cleaned system, no moving parts, directly built into the pipelines, low pressure losses.
Kyowa Hakko Bio monitors vibration trends with Yokogawa's Sushi Sensors to prevent unexpected equipment failures.
By using eServ, sensor data and maintenance information are shared with everyone involved in manufacturing.
Bushu Pharmaceuticals, Ltd., a major contract manufacturing company, is working to eliminate human error to ensure the integrity of test results data, and to promote reliable inspections and paperless operations.
Establish thorough quality assurance with state-of-the-art facilities and technologies to foster the future of medical products.
At Shionogi, the facility maintenance management system eHOZEN, the pr edecessor of eServ, has been used for about 10 years. However, due to the aging of servers and systems, they have begun considering renewing the system with the latest one. When considering this, suggestions from several vendors were received assuming that the system package safely migrates data assets accumulated on the current server and meets the following requirements:
The introduction of eServ has resulted in a centralized system of facility information. The reason for the loss of production opportunities has become clear, and it has become possible for all members to follow up the progress of the measures.
Wide and Clear
Confocal Scanner Unit
- For remote monitoring (of temperature, pressure, and flow volume), installing the SMARTDAC+ GM in the plant and the SMARTDAC+ GX in the office provides for a scalable, pc-free on-site data monitoring solution.
- You can centralize management of large quantities of data by automatically transferring acquired data to a FTP server.
The discharge of improperly treated industrial chemicals and fuel gas can have a major impact on the environment, posing a serious threat to public health. Concurrent with the global growth of manufacturing operations to keep pace with market trends, many countries are taking measures to deal with environmental problems.
Cell stage categorized using FucciTime lapse imaging of Fucci-added Hela cells was conducted over 48 hrs at 1 hr intervals. Gating was performed based on the mean intensities of 488 nm and 561 nm for each cell. They were categorized into four stages, and the cell count for each was calculated.
For the management of raw materials in the pharmaceutical and cosmetics industries, a manual titration method presents many difficulties. Yokogawa developed the NR800 FT-NIR Analyzer, and with this system, measurements are reliable and stable. It is much easier to control quality.
Faster, Brighter, and More Versatile Confocal Scanner Unit
- Colony Formation
- Scratch Wound
- Cytotoxicity
- Neurite Outgrowth
- Co-culture Analysis
- Cell Tracking
Eliminating the wire using wireless transmitter is the perfect solution for rotating equipment. It establishes data collection between the transmitter and the gateway by reliable communication even though the dryer was rotating.
SMARTDAC+ GX series records the clean room temperature, humidity, atmospheric pressure, door openings and closings, etc.
This introduces a system that uses Ethernet communications to acquire measured values, target values, and control output values from a controller installed on site into a PLC at high speed (ten units' worth within one second).
A critical requirement in biopharmaceutical development is the integration and automation of process equipment and analytical instruments used in the laboratory. Bioprocess labs with multiple lab-scale bioreactors often execute cultivation experiments in parallel for research or process development purposes.
As part of a collaboration between Securecell (Zurich, SW) and Yokogawa Life Science (Tokyo, Japan), this application note demonstrates the effective use of the Lucullus® Process Information Management System (Lucullus®) to assist in the control of three Advanced Control Bioreactor Systems (BR1000) to study glucose utilization of CHO cells for optimal monoclonal antibody productivity.
In semiconductor manufacturing processes, a deficient clean room environment can lead to defects and wasted resources, making a strictly controlled clean room indispensable. Maintaining the environment in the clean room requires control of air filters, HVAC systems, room temperature, humidity, airborne particles, and other factors.
In the plants of food and beverage manufacturers, there are times when monitoring and recording of production equipment is necessary inside clean rooms. This is an introduction to monitoring and recording in clean rooms using paperless recorders.
Performing control while changing the set point temperature moment by moment is called running a program pattern (or simply running a program). Sterilization and pasteurization require maintaining specific temperatures for specific durations.
The paperless recorder DX series automatically calculate the Fo value from the heating temperature and are useful in managing the sterilization process by displaying and recording the value together with the heating temperature.
In the manufacturing process of Pharmaceutical, Chemical and Food & Beverage industries, the cleaning and sterilization of tanks and piping are done with various cleaning solutions, fresh or hot water and steam after manufacturing products. Clean-In-Place (CIP) is the system designed for automatic cleaning and disinfecting.
By using the Multibatch function (an option added with SMARTDAC+), you can efficiently record data from multiple devices onto a single SMARTDAC+.
Fluorescent ubiquitination-based cell cycle indicator (Fucci) is a set of fluorescent probes which enables the visualization of cell cycle progression in living cells.
Monitoring of Soundness of Power Supply Bus Bar (In-vehicle Lithium-ion Battery Applications)
Using the custom display function that comes standard with DXAdvanced means that you can combine the recorders, displays, and switches used in various kinds of equipment.
Using the batch name + lot number system, past measured data can be recalled for reference by batch name.
- Universal inputs provide support for thermocouple, RTD, voltage, and a variety of other input signals.
- Lineup of models for up to 450 inputs.
Allows multipoint monitoring and recording on a single unit. - Easily enables network-based data management.
file transfers, Web monitoring, and alarm e-mail
By using the computation function of the SMARTDAC+ series Paperless recorder GX/GP, computation option computes the "F-value," or sterilizing value for the sterilization process, so that the computation results can be recorded in the form of data.
The sterilization temperature prior to the filling process is monitored in the field or office. The temperature data is recorded in an external storage medium.
Blending plays a key role in industries such as food, healthcare and chemicals etc. Temperature and vacuum measurements are very important in minimizing the moisture content to ensure the quality of the final product. Strictly maintaining them throughout the process ensures the final product yield.
One of the primary applications for high purity water is for boiler feed water. The measurement of pure water pH can be one of the quickest indicators of process contamination in the production or distribution of pure water. Effective chemical treatment of the feed water is vital in maintaining the useful operating life and minimizing maintenance costs of the boiler.
Industry:Power, Pharmaceutical, Common
With industrial and economic development comes increasingly large and advanced power plants and factories. Nevertheless, we find many cases where the original cables, cable tunnels, and other components of the power infrastructure have languished under continuous operation.
This technical white paper will discuss Yokogawa's CENTUM VP DCS (Distributed Control System) product, hereafter referred to as "CENTUM VP", and the extent of its compliance with Part 11 of Title 21 of the Code of Federal Regulations, (21 CFR Part 11), the Electronic Records / Electronic Signatures Rule.
The worlds of process automation and production management have been converging for some time. What once used to be islands of automation and production management functionality connected through highly proprietary integration schemes that were costly to maintain have developed into integrated platforms that provide seamless data exchange between the world of automation and the plant floor, the functions of production and operations management, and integration with business level systems.
The world of process automation is governed by procedures. While we like to refer to the process industries as being largely "continuous", this could not be further from the truth. Process manufacturing is constantly in flux.
From engineering to installation, commissioning, operations, and maintenance, FOUNDATION fieldbus offer significant cost reductions of 30 percent or more versus conventional analog systems. Many of these cost reductions come from the advanced functions that fieldbus offers versus analog technology.
This document describes the operation and data flow of the Yokogawa Print Wave software using the DX-P Reporter. It will provide a detailed explanation of the Advanced Alarm Reporter functions. The functions described in this paper were first released in Print Wave version 5.5.
Discovering your Baseline with OT Security Risk Assessment
The first stage in creating next-generation production control system that achieves innovative plant operation is providing "Visualized operation". "Visualized operation" for the customer means that he can reliably access and visualize plant data regardless of plant location and time.
Manufacturers that are digitalizing lab information management can improve quality and streamline operations. Read the complete article inside.
Lonza's Riverside plant manufactures bulk active ingredients for the pharmaceutical industry. A new, fully automated multipurpose reactor train was installed in early 1996. The train includes ten 500 to 1500 gallon vessels used for reaction, distillation, phase separation, and crystallization; two centrifuges for isolating finished products; and two dryers.
The critical steps in achieving advanced process control include building an accurate digital twin of a bioreactor, validating it, and establishing communication between the bioreactor and its digital twin. Several of these steps are already mature and Yokogawa is making rapid progress toward realizing ‘smart’ bioreactors for smart manufacturing.
Yokogawa Electric began offering the environmental monitoring system "OpreX Environmental Monitoring System" (hereinafter, OpreX EMS) for the pharmaceutical and medical device industries in October 2020. OpreX EMS, which was launched simultaneously domestically and overseas, is based on customers' needs, such as regulatory compliance, diversification of operational risks, and high usability. When asking the person in charge about the development history and features of the product, it was found that it is a new solution that meets the company's business vision.
Exploring the technologies needed to achieve automatic control of cell culture processes.
Unlocking the Keys to a Sustainable Pharma Supply Chain
Yokogawa Insilico Biotechnology released its Insilico Digital Twin Factory, which can help drugmakers increase productivity and bring down manufacturing costs and time to market by potentially replacing up to 50% of the experiments needed during the process development, characterization and scale-up of biopharmaceuticals.
Assets and operations will have human-like learning and adaptive capabilities, allowing responses without operator interaction to situations within a secure, bounded domain.
The use of optical fiber for temperature sensing is expanding beyond safety applications.
The wireless standard LoRaWAN enables wireless communications and digital transformation over long distances, supplementing in-plant wireless networks such as ISA100.
Cloud-based wireless sensing enables safety, reliability, and profits through widespread asset monitoring.
Process automation systems are increasingly connected to IT systems and the outside world, introducing cybersecurity concerns, which can be addressed using techniques such as software-defined networking and monitoring services.
Asset management plays a key role in operational safety, and it is critical to capture and transmit these data in a secure, digitized way to ensure that they are up to date, accurate and easily accessible.
Robots have long been used in discrete manufacturing and machine automation applications, and their use is now spreading to address process industry applications.
Historians provide the data storage, secure connectivity and built-in tools required for implementation of digital transformation initiatives.
Downloads
Videos
Connecting MES and DCS in your pharma or biotech factory: Werum PAS-X MES and Yokogawa CENTUM VP
The Yokogawa business vision states that the company endeavors to achieve Net-zero emissions, ensure the Well-being of all, and make a transition to a Circular Economy by 2050.
YOKOGAWA will contribute to technology evolution particularly in measurement and analytical tools to help build a world where researchers will increasingly focus on insightful interpretation of data, and advancing Life Science to benefit humanity.
By equipping SMARTDAC+ with the advanced security features option "/AS", it meets the strict requirements of the U.S. FDA 21 CFR Part 11 and supports DI in compliance with PIC/S and ALCOA+ by WHO, MHRA and FDA.
Our approach is to leverage state-of-the-art technologies for real-time monitoring and predictive control that allow virtual environments where "digital twin" processes can provide distinct advantages.
By adopting the environmental monitoring system, we were able to create an environment in the cell storage facility that allows for quality control, maintaining a high level of safety.
Yokogawa leverages our extensive knowledge and experience in IT, operation and control technology to build an advanced improvement cycle that is useful to all management levels, and eventually aims to achieve Pharma 4.0 together with our customers.
In this webinar, Professor Jonny Sexton discusses a pipeline, developed in the Sexton lab, for the quantitative high-throughput image-based screening of SARS-CoV-2 infection to identify potential antiviral mechanisms and allow selection of appropriate drug combinations to treat COVID-19. This webinar presents evidence that morphological profiling can robustly identify new potential therapeutics against SARS-CoV-2 infection as well as drugs that potentially worsen COVID-19 outcomes.
News
-
Press Release Jun 22, 2023 Yokogawa to Release OpreX Informatics Manager, Enabling Integrated Management of Experimental Data and Research Resources in the Cloud
-
Press Release Feb 20, 2023 Yokogawa Enters into Partnership with Radial Software Group to Provide AI-powered Viewport Software Worldwide
- Giving customers a single view of all their technical data -
-
Press Release Feb 2, 2023 Yokogawa Acquires Fluence Analytics, a Pioneer in Digitalizing the Monitoring of Polymerization Reaction Processes
- Enabling continuous real-time monitoring of polymers and biopolymers -
-
Press Release Apr 1, 2022 Notice of Commencement of Business of Pharmira Co., Ltd., a Joint Venture for Contract Development and Manufacturing of Active Pharmaceutical Ingredients and Intermediates
-
Press Release Nov 2, 2021 Yokogawa Acquires Insilico Biotechnology, Developer of Innovative Bioprocess Digital Twin Technology
- Enabling solutions for biopharmaceutical development and production -
Looking for more information on our people, technology and solutions?
Contact Us