Visual MESA® Supply Chain Scheduling software provides future visibility through detailed simulation models of both logistic and unit operations, keeping constantly updated projections of inventories and material properties.
Click here to learn about Visual MESA Supply Chain Scheduling
Key areas for Operational Excellence Transformation
Operational Excellence Transformation is Yokogawa and KBC’s co-innovated portfolio of solutions and services.We provides comprehensive solutions for business automation in all four areas using consulting and digital technology.
Supply Chain Optimization
Supply Chain Management deals with satisfying customer demands by selecting the most appropriate feedstocks the plant can process efficiently, and delivering the products to the customers with maximum efficiency. Today, most of the industry SCM solutions are executed manually and/or separately. In most cases, specialized planning and software packages that have been implemented previously are not connected to other systems, such as sales and distribution and real-time production systems. As a result, the benefits of SCM are not fully realized.
Yokogawa's strategy to improve supply chain management starts with defining the corporate long-term strategy and aligning it with operations, maintenance and all other functions involved in the entire value chain. It includes:
Key Operational Competencies in Supply Chain Optimization
- Term Contract Planning: Commercial and economic evaluation of long-term contract obligations
- Supply Chain Planning: Economic optimization of the hydrocarbon supply chain for short-term, mid-term, long-term and strategic time horizons
- Price Deck Formulation: Generate price forecasts based on optimization boundaries and time horizons for feedstock and products
- Supply Chain Scheduling: Schedule optimized operations (process inventory and blending) over time, taking logistical constraints into account
- Commercial Contracting: Develop and negotiate favorable and competitive contract terms for feedstocks and products
- Inventory Management: Measure and reconcile the amount of each product made and raw materials consumed to produce an accurate material balance through production accounting and oil loss measurement
Yokogawa's approach to supply chain management involves digitalizing operations from supply to distribution. We then adopt the identified end-to-end optimization strategy to discover and manage all hidden costs (wastes) in the long chain. Our main objective is to find the Global Optimum to enable Just-in-Time in manufacturing and delivery for suppliers and customers, using minimum inventory and movement.
By applying digital technologies onto the end-to-end process of the supply chain (manufacturing raw materials to final products and managing purchase orders to good receipts), we may be able to improve the following:
- Customer & Supplier Experience: Deliver personalized engagement with an improved understanding of the product value directly to customers and suppliers
- End-to-End optimization: Extend the optimization horizon using real-time information on supplier delivery and customer demand across organizations and companies involved in the long supply chain
- Information Mobility: Enable optimal delivery and visibility by tracking personal location and activities with mobile technology
- Predictive Insights: Anticipate demand, supply and asset requirements with better insights
- Digital Business: Improve overall business agility and borderless collaborations by eliminating internal information silos
By combining Yokogawa’s product portfolio and KBC’s consulting services, we provide our customers best practices and domain knowledge that empower them to improve their operations, as well as a digital platform that supports such activities and initiatives. Our Operational Risk Management scope does not only cover partial improvements in the organization, but also optimizations in plant operations to achieve continuously improving safety, reliability and operability.
·Asset Operations and Optimization
- Optimize the potential of physical assets, by pushing throughput and maximizing the production of the highest value products, whilst minimizing variable costs such as energy.
- Deliver small and large capex projects, on time and on budget, to deliver growth and meet environmental requirements.
·Operational Risk Management
- Reliably control safety, health and environmental risk at a personal and process level. This assures the robustness required to avoid catastrophic losses.
·Asset Management and Integrity
- Confidently ensure asset reliability and availability, whilst controlling maintenance costs. This assures the asset always meets expectations and is always available to capitalize on short term market opportunities.
Visual MESA Supply Chain Scheduling
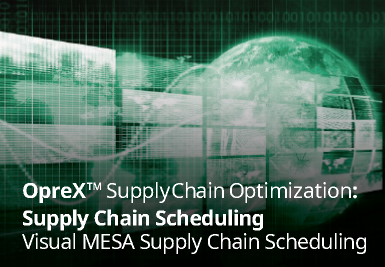
Almost every company in the process business has the ability to create an economically efficient operations plan to balance supply and demand. Managing scheduled operations through a systematic business process supported by effective analytical tools is crucial to achieve the benefits of optimized operations planning.
The process objective is to:
- Maintain a detailed schedule of operations that follows as close as possible to the planned targets
- Monitor current operations progress and environmental status to capture potentially disruptive events
- Decide if a revision of the planned targets is needed, then replan
- Otherwise asses the impact of events in terms of deviations from planned targets
- And then establish "surgical" modifications to the operations schedule aimed to attenuate the impact of disruptions
Operability Improvements in Event Management: Predict, React, Minimize
The key for keeping adherence to an optimized plan is to:
- Predicts the occurance of disruptive events and therefore to establish proactive actions minimizing further deviations
- Quickly and precisely analyze corrective actions to cope with the occurrence of events that were not anticipated
- To get visibility on the future effect of the corrective actions to be implemented, avoiding that today's solutions become disruptions short after
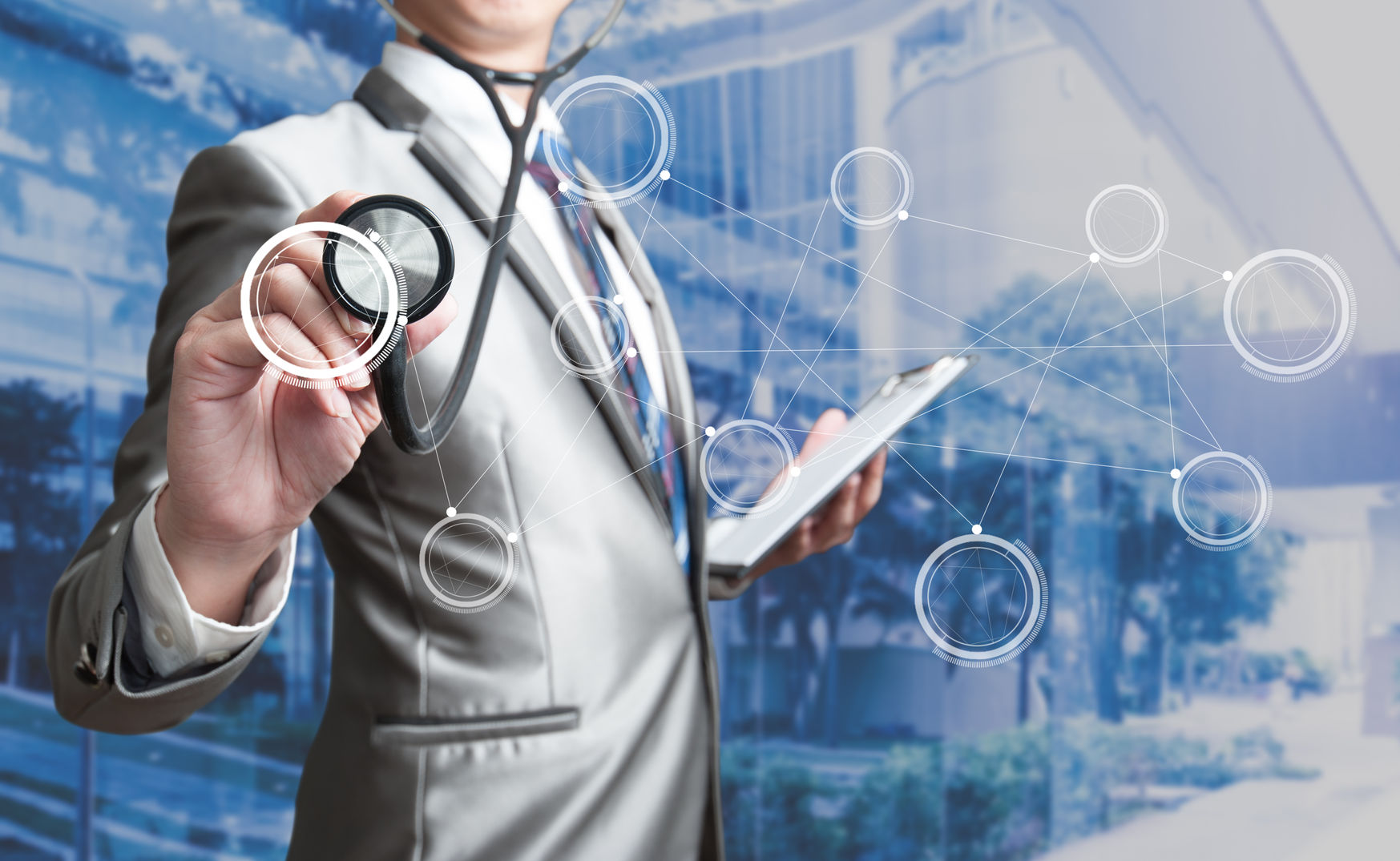
Summary of Supply Chain Scheduling Capabilities
- Evergreen outlook/projections of operations
- What if analysis support
- Efficient Infeasibility management
- Planning Targets Tracking
- Rolling Horizon, Non-Regular Time Granularity
- Goal Oriented Task and Automation
- Flexible user Defined Visualization
- Discrete Event and Continuous Simulation
- State Even Detection Control
- Integrated Supply Chain Model
-Logistics - feedstock and product tank yeard - and Operation Simulation
Support for Collaboration
- Visual MESA Supply Chain Scheduling supports the collaborative scheduling among different users working on an integrated model of the whole supply chain.
- The model is segmented in areas under the responsibility of different decision makers defined through user profiles with read or write permissions to different model areas.
- Every user is allowed to introduce changes only to the enabled area but can analyze the propagating effect of everybody’s scheduling decisions.
- Each scheduler can maintain different schedule scenarios to perform private what-if analysis and collaborate with others to consolidate a unique consensus schedule that is published for everybody to consult.
Dock Scheduling Assignment of Jetties/Berths
- Visual MESA Supply Chain Scheduling Dock Scheduling supports the scheduling and simulation of load/unload operations in berths and jetties.
- The schedule can be managed by editing in a single-click, user-friendly table containing all the detailed operation information: vessel estimated arrival times, vessel data, order data, loading/unloading facilities (berths, jetties and tanks), materials, quantities and rates.
- Timing and allocated resources for the dock scheduling can also be edited through and interactive Gantt diagram allowing “drag and drop” edition.
- It is possible to manage multi-movement (sequential or simultaneous load/unload from/to different tanks) and multi-compartment vessel operations.
- Automation rules are provided to generate ship nominations in order to fulfill feedstock replenishment and products lifting of a given production plan and inventory policy, allocating available berths.
- It provides comprehensive operation reports and can be integrated with other systems such as importing vessel updates from navigation control systems or exporting berth schedule to operation execution system
Blending and Scheduling
- Visual MESA Supply Chain Scheduling provides also detailed model for event-based scheduling of blending operations that allows to capture the logistics aspects of blending facilities
- Is integrated with the production and delivery schedules for end-to-end supply chain analysis, provides rich visualization of blending operation’s outlook and uses simulation to support the detection of disruptive events
Multi-Blend Schedule Optimization
Visual MESA Supply Chain Scheduling Multiblend Schedule Optimization supports the definition of optimal recipes and blend volumes for several products in a window of time.
The recommended volumes and recipes match the supply and demand forecast, meet the constraints regarding storage capacity, product specifications, recipe limits and blending capacity and are decided by minimizing the total cost of the campaign or minimizing the quality giveaway.
Blend properties for products are calculated using non-linear mix equations and the model solution search is based on an MILP solver
Find more details on this page
Cerchi più informazioni su tecnologia, soluzioni o sulla nostra squadra?
Contattaci